The Ten Golden Rules of GMP
What is GMP? The WHO defines GMP as preventing errors that can't be eliminated through QC of the finished product. Learn about the ten golden rules of GMP.
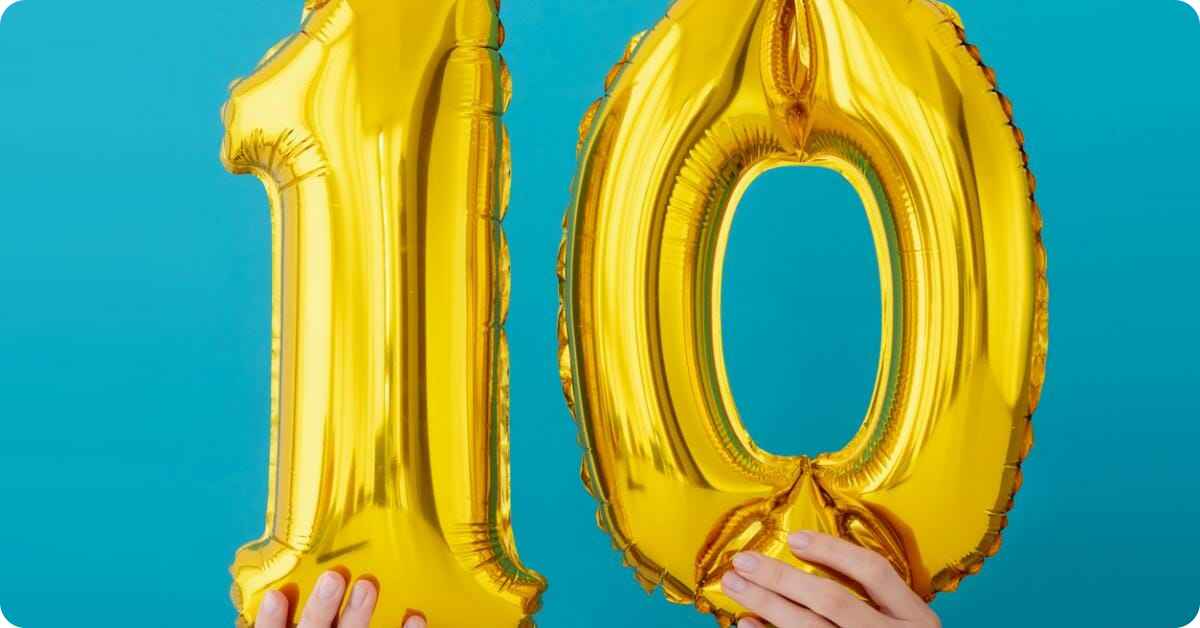
What is GMP?
The World Health Organization defines the GMP as follows; GMP prevents errors that cannot be eliminated through quality control of the finished product. Without GMP it is impossible to be sure that every unit of a medicine is of the same quality as the units of medicine tested in the laboratory.
Prevention is key in GMP
The WHO’s definition is simple and clear; prevention is key. We cannot test every tablet, vial or capsule that is distributed to patients worldwide. To make sure that companies understand the GMP’s and it’s requirements there are numerous documents (guidances). Most major economic blocks have their own GMP; the EU has it’s EudraLex and the U.S. has the FDA Code of Federal Regulations. The World Health Organization (WHO) publishes it’s GMP regulations in a set of documents called “Technical Report Series”.
All these documents stress that you must take GMP into account from the very start, whatever you are doing:
If you buy a piece of equipment for a cell line, you must qualify it before you actively use it for production purposes,
If you get a new granulate supplier, you qualify that supplier,
When you buy a new computer system, you must perform computerized systems validation.
Etc.
Reading through the GMP documents you may lose the overall picture. What do I need to do to prevent errors that cannot be eliminated through QC of the finished product? This is why we have compiled the ten golden rules of GMP. These golden rules are contained in our GMP Basics course in a handout to trainees.
The ten golden rules of GMP
Design the facility according to the GMP requirements, from the very start. This should be common sense. But it’s extremely hard to get it right without extensive planning. Companies must invest in both time and resources to get a first-time-right facility.
Validate processes, Testing is key in the GMP. You validate everything that’s intangible; software, your production process and cleaning. You must provide documenten evidence that your process / software produces the same results, consistently.
Write great procedures, and follow them, We must not forget our audience when writing procedures. Apply the Good Writing Practice rules for GMP documents and make your procedures easy to follow. Besides that, invest time in your employees. Compliance follows comprehension.
Identify who does what, Make organograms, job descriptions and discuss responsibilities with your team members. Have clear reporting structures and make sure that they are adhered to. Confusion can lead to a drop in compliance.
Document everything properly, Good Documentation Practices (or GDocP in short) must be followed to achieve a Pharmaceutical Quality System that meets the requirements of the international GMP’s. When everything is documented properly you can always trace what happened, and where. Although documentation may sometimes be deemed trivial by process operators many mistakes still happen between shift transfers or by scribbled notes.
Train and develop your staff, Update your staff regularly on the latest GMP developments, WHY we have the GMP’s and WHY they are so important to ensure patient safety. Don’t forget to include the business case while training; high quality leads to fewer defects and happy customers. This will in turn lead to an increase in job satisfaction and less painful conversations with QA / QC.
Keep good hygiene practices, Everything gets dirty, always. That’s why cleaning is so important. Dust settles, equipment generates particles and humans do too!
Maintain and upgrade buildings & equipment, Besides getting your equipment and facilities right the first time, they won’t stay like that forever. The GMP requires you to be state-of-the-art. This includes preventative maintenance and regular investment in new equipment and technologies.
Embed quality in the entire product lifecycle, By focusing on all aspects of the product lifecycle you future-proof yourself against any potential problems which may be far, far away. The lifecycle of a pharmaceutical product can be extremely long, meaning a lot of things can go wrong at any step. GMP may only apply to production and import, but it’s principles can be applied to any product phase (where other guidances like the GLP / GCP may fall short).
Perform (internal) GMP audits regularly. Check yourself regularly by performing internal GMP audits at intervals. Rotate auditors, points of focus and the schedule. If you always check the same things you’ll never significantly improve your GMP compliance level.Â