Defining the Undefinable: Quality Culture
People want a neat definition, a tidy checklist, or a set of metrics to measure quality. But when you peel back the layers, it becomes clear that “Quality Culture” is more of a broad vision than a well-defined endpoint.
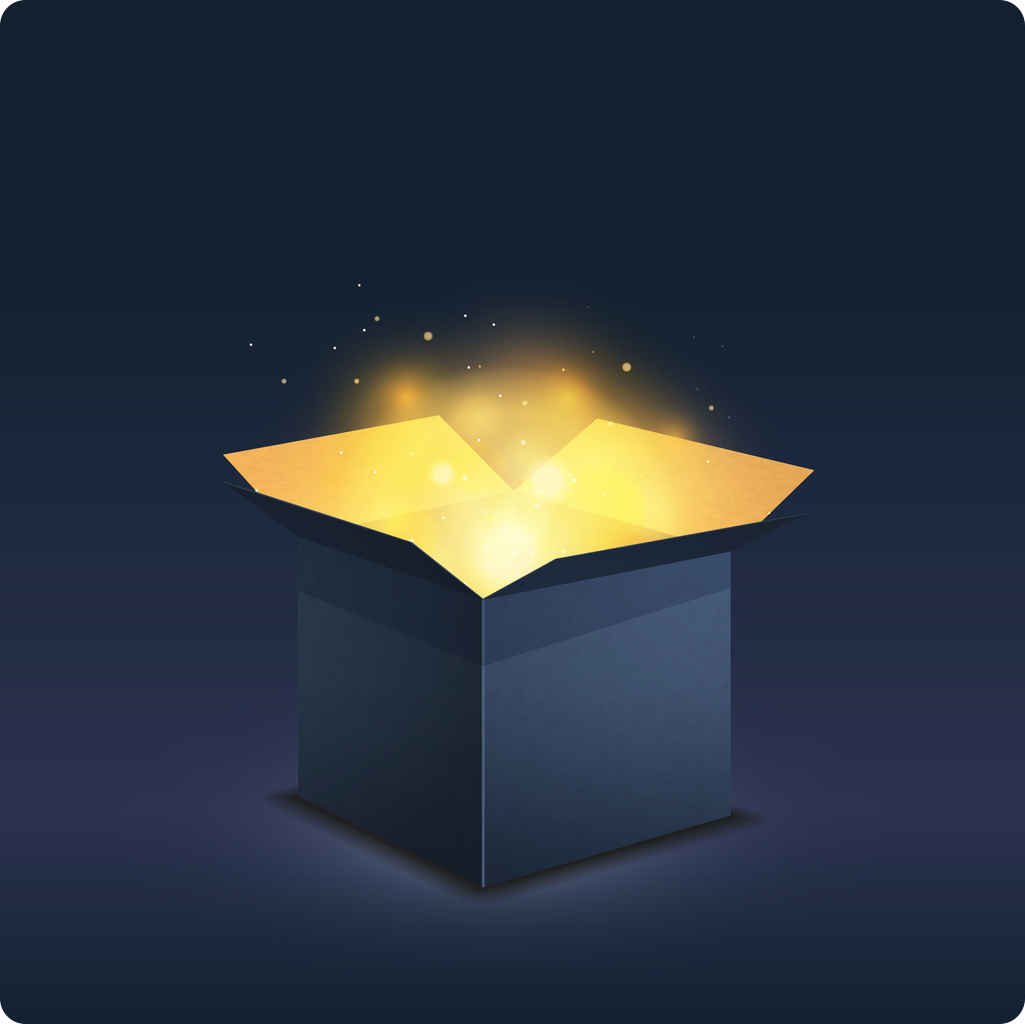
At Pharmaceutical Consultancy Services (PCS), we’ve spent many hours implementing and refining something that’s popularly called “Quality Culture.” If you’ve heard the term, you already know how ambiguous it can be.
People want a neat definition, a tidy checklist, or a set of metrics to measure quality. But when you peel back the layers, it becomes clear that “Quality Culture” is more of a broad vision than a well-defined endpoint. It’s a classic “container-statement,” filled with different interpretations depending on who you ask and what perspective they bring.
Even so, the pharmaceutical industry repeatedly tries to treat “Quality Culture” as a straightforward concept, and the resulting confusion does more harm than good.
Over the years, regulatory agencies have tried to measure culture through “Quality Metrics.” At best, these metrics offer a snapshot of outcomes—warning letters, 483s, compliance flags. While such data might highlight trouble areas, it doesn’t tell you how to navigate toward sustained positive results.
You’re left trying to fix problems after they emerge, instead of shaping and guiding behavior in a way that prevents issues in the first place. It’s like reading accident reports to figure out how to drive more safely—useful, but hardly a blueprint for how to be an excellent driver.
The truth is, there’s no official GMP guidance that outlines how to “get” a Quality Culture. The guidance documents and regulations tend to define outcomes more than they describe the journey to achieve them. That’s why we at PCS draw on best practices beyond pharma, looking at how other industries create robust systems and shape strong organizational values. Sure, we keep an eye on 483s and warning letters—we need to know what’s going wrong. But we’re more interested in asking: Why did it go wrong? How do we fix it at its root? What does our organization need to shift or strengthen so that it won’t happen again?
In our work, we see too many companies focus solely on compliance. They paint the house’s exterior to hide cracks in the walls, convinced that if it looks good, it is good. But that superficial approach never holds up when you’re dealing with complex manufacturing controls and the underlying organizational behaviors that lead to real quality.
You can’t simply mandate “quality” from the top, any more than you can expect a team to guess what good culture looks like. It takes a reality-oriented approach: start by understanding your actual day-to-day activities, your processes, your people’s challenges. Once you understand that reality, you can build compliance seamlessly into each step.
We know these cultural shifts can be daunting. Everyone wants that big banner saying “We Have a Quality Culture!” But the actual path toward creating and sustaining it is more nuanced and gradual.
A bright sign in the hallway or a mission statement pinned to the wall doesn’t magically change behaviors. True transformation requires honest self-assessment, transparent dialogue, and iterative improvement grounded in the real workings of your organization. Only then can “Quality Culture” move from a vague aspiration to a tangible way of doing business that meets regulatory standards and elevates performance.
As we continue to research and write—yes, we’re still penning our own book on this topic—the one consistent piece of advice we share with clients is to embrace the complexity. Accept that “Quality Culture” is more about the journey than a neatly prescribed formula. Keep looking outside traditional frameworks, be open to adapting ideas from other industries, and never lose sight of your own operational reality. In our experience, that’s the surest way to cultivate the culture that not only meets GMP requirements but truly transforms an organization from within. And once you shift from simply “looking compliant” to actually being compliant, the difference is night and day.